About
For over 80 years, the concrete industry has been trying to control and reduce concrete build up in ready mix trucks...
.... we are the revolution.
To date, nowhere in the world has there been a commercially viable and safe way of stopping this build up and it is considered that the problem is getting worse, with the addition of the many new additives and fibres to assist with stronger and faster curing concrete.
After unsuccessfully searching the world for a suitable system DrumBlaster was launched in 2014.
Between 2014 and 2017, DrumBlaster and Thoroughclean’s engineering department conducted field tests to prove the DrumBlaster would clean the drums efficiently and reliably using recycled water.
As part of this development, DrumBlaster conducted trials in Sydney, Melbourne, Amsterdam and Houston TX which have all been successful. All sites have produced a similar reduction in the build up of concrete by 85% or more.
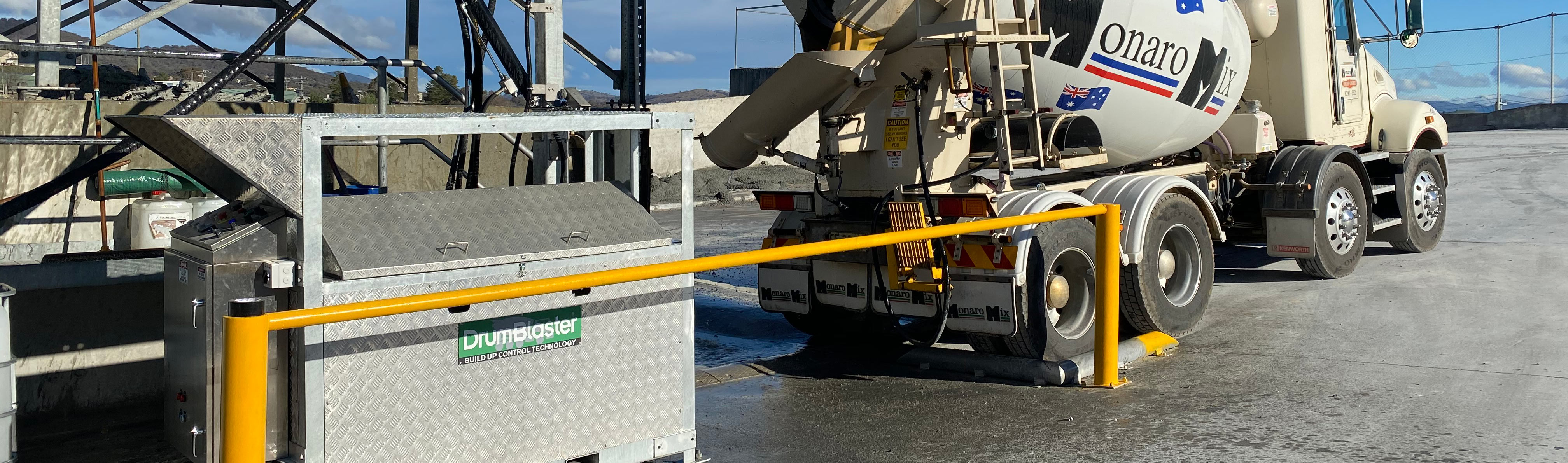
The Management Team
Jonathan Sweet
Director
Jonathan has been involved in the high-pressure water jetting industry for 20 years, developing his experience in the oil and gas industry and later in petrochemical and concrete demolition. Jonathan was involved in resurrecting the industrial services division of Programmed Maintenance Services Limited, growing the business tenfold, then setting up new businesses in Adelaide as well as the high pressure divisions in New South Wales and Queensland. Over the last 10 years, Jonathan has established a market for DrumBlaster operating in USA, UK, Europe, Hong Kong and Australia. Jonathan’s expertise in Sales and Marketing and manufacturing process has been the driving force behind the metamorphic rise of the DrumBlaster from the manually operated machine to the Automated system today, V4.
Jim Simpson
Director / CFO
Jim is an original shareholder of Drumblaster Pty Ltd and as Company Secretary handles the administrative work of the business. He holds a Commerce Degree from the University of New South Wales and post-graduate qualifications in Financial Analysis.
For more than 50 years, Jim has owned and managed a diverse range of businesses, including those in the building industry. As a licensed builder, he has developed and completed many medium density housing projects. Jim also has a special interest in start-up companies, with an emphasis on new technology and recognises Drumblaster as the new revolution in build-up control technology.